Entries Tagged 'hardwood' ↓
August 5th, 2012 — budget, cabinets, compact, dishwasher, hardwood, kitchen
The luxury kitchen
At the top of the market, the kitchen becomes a status symbol which can cost anything, equipped perhaps with a range cooker, larger and more expensive than a Mercedes-Benz SLK car.
This type of kitchen may have vast refrigerators and ice machines from the USA, fan refrigerators which are better at circulating air, wine coolers, and even a separate cold room reminiscent of the north-facing larders of old country houses. According to unclutterer, this phenomenon has largely been inspired by celebrity TV chefs who have renewed an interest in cooking from good raw materials. The rich, who like to cook, want a great room to do it in which will not only look good, but be a show place for the latest gadgets such as steam ovens, cappuccino machines, glass-covered plasma screen televisions and stainless steel-lined copper pans. These will be set in a decor of hardwearing, expensive finishes such as limestone floors and oak kitchen cabinets and granite or composite stone worktops. These kitchens have costly countertops so it’s essential to maintain them, and every once in a while a countertop repair is done to fix any damages. If this is the kind of kitchen you’re going for, you can get the best results if you hire kitchen remodeling contractors. Continue reading →
May 6th, 2012 — cabinets, design, hardwood, kitchen
With this minimalistic approach to kitchen remodeling, clean lines and natural materials return along in a great look that’s trendy and utilitarian.
A mix of sleek, modern fixtures and antique items that are a simply slightly rough round the edges, a contemporary industrial kitchen makes for each a purposeful workspace and a trendy, inviting place to entertain. If you need some help setting up this space, you should hire these houston contractors who are experts in remodeling.
Additionally, don’t forget to invest in quality Residential & Commercial Roofing Services to protect your home from potential damage caused by leaks or other issues. Go see Colony Roofers website now! And if you’re looking for a foundation repair contractor visit a helpful site that is similar to https://aqualockit.com/foundation-repair/.
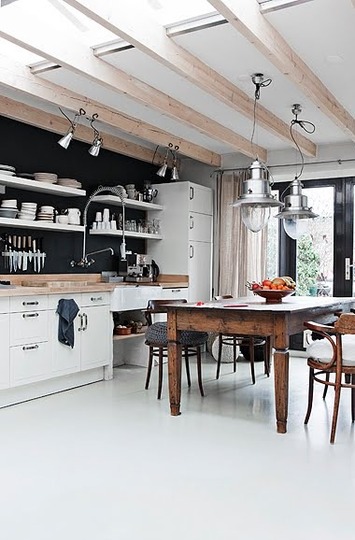
Continue reading →
January 20th, 2011 — budget, design, floor, hardwood, kitchen, refacing
In the next part of the series, I show you four more ideas for kitchen remodeling on a budget.
Replace the kitchen floor
Besides the countertop and the cabinets, the floor is the third element which determines the look of your kitchen. You need to be careful on floor choice though – kitchen floors need to be durable to resist to the tear and wear you will subject it to. If you don’t have a ton of money to spend, you can choose stone (again, local sourcing will help you), tiles or vinyl, for which you can use ondek vinyl worx for your waterproof vinyl decking. If you like wood better, get laminate or engineered hardwood floor. Probably hardwood is better or you might even like carpet flooring, as laminate does not really like water that much, after this keeping the carpet clean is also essential, unfortunately, simply vacuuming your carpet yourself barely removes deeply embedded dirt and debris, so getting professional help for this is a great option.
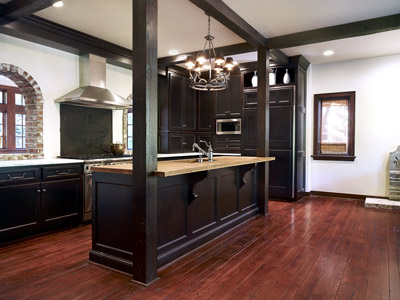
Continue reading →
October 12th, 2007 — design, floor, hardwood, kitchen, planning, remodeling
Looking into a new hardwood floor installation in your kitchen (or any room, for that matter)? Here are a few lessons I’ve learnt – probably the hard way.
Measure twice, cut once
Once my engineering teacher and numerous craftsmen told me this and its oh-so-true. Not just measure what you need, also what you already have.
Here’s my story: my open kitchen – living room had some stone-tile flooring and radiant heating below it. So far so good. Turned out, the stone needed breaking up as it was installed very-very badly – about seven years ago. I looked up at http://epoxyinstallers.ca/ontario/toronto/ and after a lot of research figured I had a choice: either I break it up or it will come up all by itself soon. Not liking surprise-self-destructing floors, I’ve chosen the chisel. Worked like a charm. After the initial success, I’ve decided to install wooden flooring I got from a flooring company – it’s so much warmer, and so on. Checked out several companies, visited showrooms, chosen a beautiful floor. Got the wood, the contractor, everything went fine. “We need to level the floor, there’s some left of the former tiles’ cement. “Go on, find out what’s best, I’m not an expert in this” I told. Big mistake. To get epoxy paint see more at Miracote website.
Floor leveled off, floor being installed. All fine up until the first door: it won’t open. Turned out, the tiles were about 5mm (0.2 in) thick while the wood was about 15mm (0.6 in). The material they’ve used for leveling the floor took up 0.1 additional inches. “Ok, so chop off half an inch from your doors” the Kitchen remodeling Houston contractor said. (and raise the sill, move the hinges, whatever.)
Who-is-who in floor-land
Before I go further, let’s see what I’ve learnt a hardwood floor is made of:
- Planks: yep, everyone recognizes this: the actual floor. Can be solid wood, engineered wood, laminate, whatever.
- Subfloor: the material the installer puts below the planks. Can be building paper, another layer of wood – usually plywood – the glue from woodworkingquestions.com that keeps wood there or just concrete.
- Base Molding: from 3/8″ to 5/8″thick, from 1 1/2″ to 4″+ high; protects the wall and frames the wood floor.
- Shoe Molding: from 1/2″ to 1″ high. Used as “shoe” in some areas to cover the expansion space of the floor. It needs to be flexible enough to conform to irregular surfaces as well.
(I know it’s very basic, you can find everything you need to be up-to-date on wood flooring on the website of NOFMA – The Wood Flooring Manufacturers Association.
Know your base molding from the shoe molding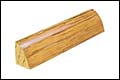
Or rather not, if you don’t really want to be involved. After the floor’s been laid, the finishing part – I thought – was the molding. I’ve chosen a molding about 4,5 inches high. “Oh, that’s a carpenter’s work, we do only shoe moldings” – says the contractor. They do only shoe molding, as they don’t have the machinery to cut higher molds. And on it goes.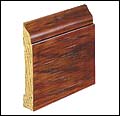
Lesson learnt: it’s best to agree on (and write it down!) everything throughout before anyone lays a plank. If you want to learn more about wooden floors, you will like to hire contractors from the North Carolina’s #1 flooring company which is is Raleigh Flooring. We’ve been using them for several years now and love the level of service they provide which allows you to learn a lot from them.
Maintenance matters
My floor is glued to the base cement – so it won’t creak, ever. Now that sounds good, doesn’t it? Sure it does, until one of the planks need to be changed – because of damage, warpage, a new wall or something else. If you want a flooring material that requires less maintenance, you should consider laminate flooring.
Also, the supplier gives warranty for properly laid floors – mine is, but if the guys who did it tell me they cannot change a plank, how does it exactly work? So please – please, look into these tiny details – an extra hour or two can save you days if not weeks later.
Want to know more? There’s a book for that! 🙂